Source Capture Hoods
Source capture of pollutants using localized exhaust hoods is an economical and cost-effective means to control plant air quality. Nuisance dust, fumes, mist, or smoke can be effectively captured and removed at the source with properly designed source capture hoods. Capturing the dirty air at the source minimizes the amount of air exhausted from the space which reduces the amount of make-up air required back into the space. Carefully designed hoods are available as standard “off-the-shelf” designs, or they can be custom designed to maximize capture of particulate and fume. In most cases, where we have not seen or applied a hood to a similar application, the starting point is the “Industrial Ventilation – A Manual of Recommended Practice for Design” manual.
Common Industrial Exhaust Hoods
Exhaust hoods provided by SysTech are custom designed to fit the application. The size of the workspace envelope, worker access requirements, capture velocity, and airstream materials help determine the design airflow. Design considerations include mounting configuration, side shields for cross drafts, materials of construction, internal baffles, open area, and capture velocity.
BACKDRAFT HOOD
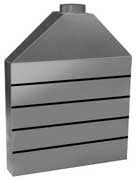
CANOPY HOOD
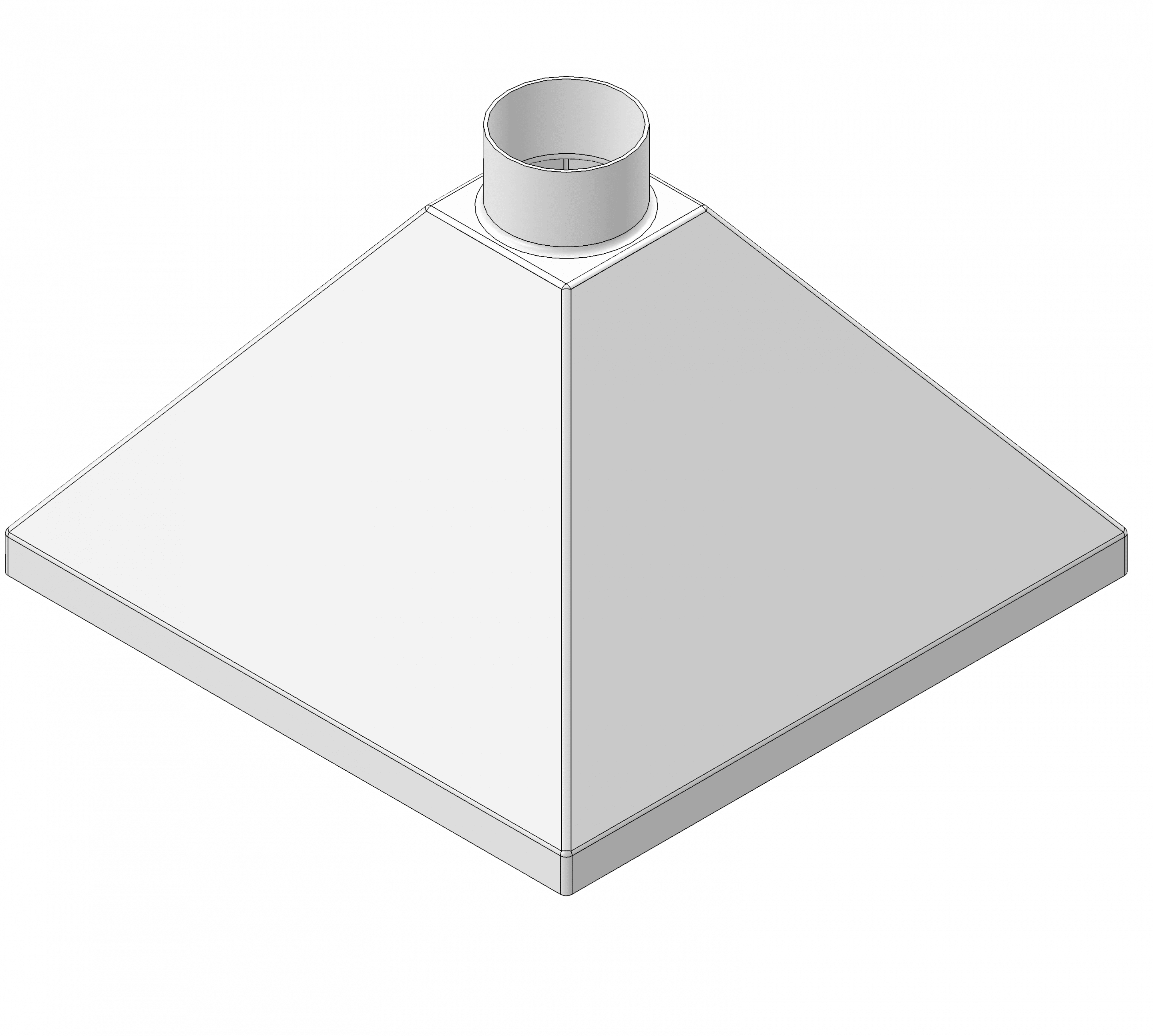
CONICAL HOOD
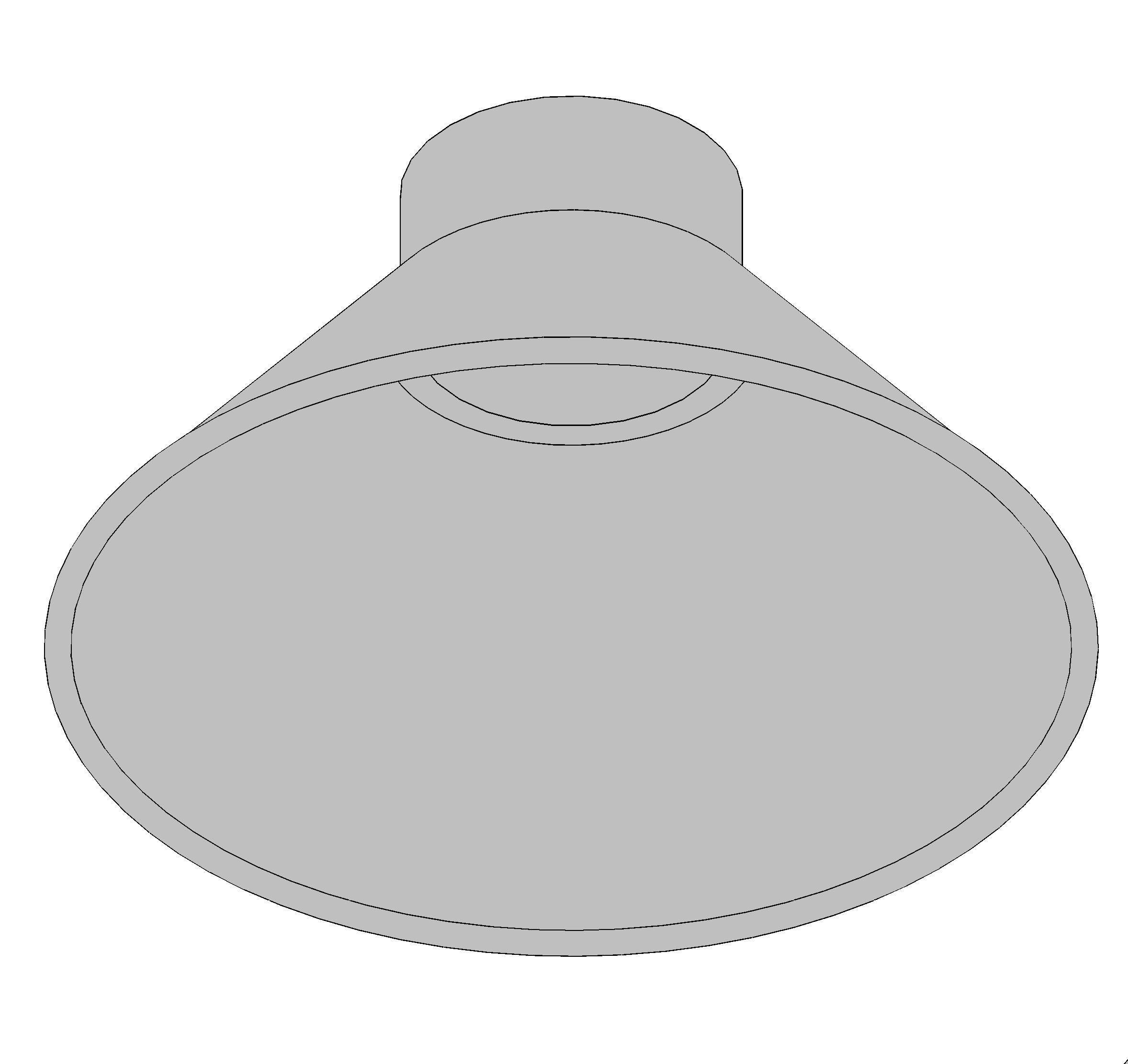
BENCHTOP HOOD
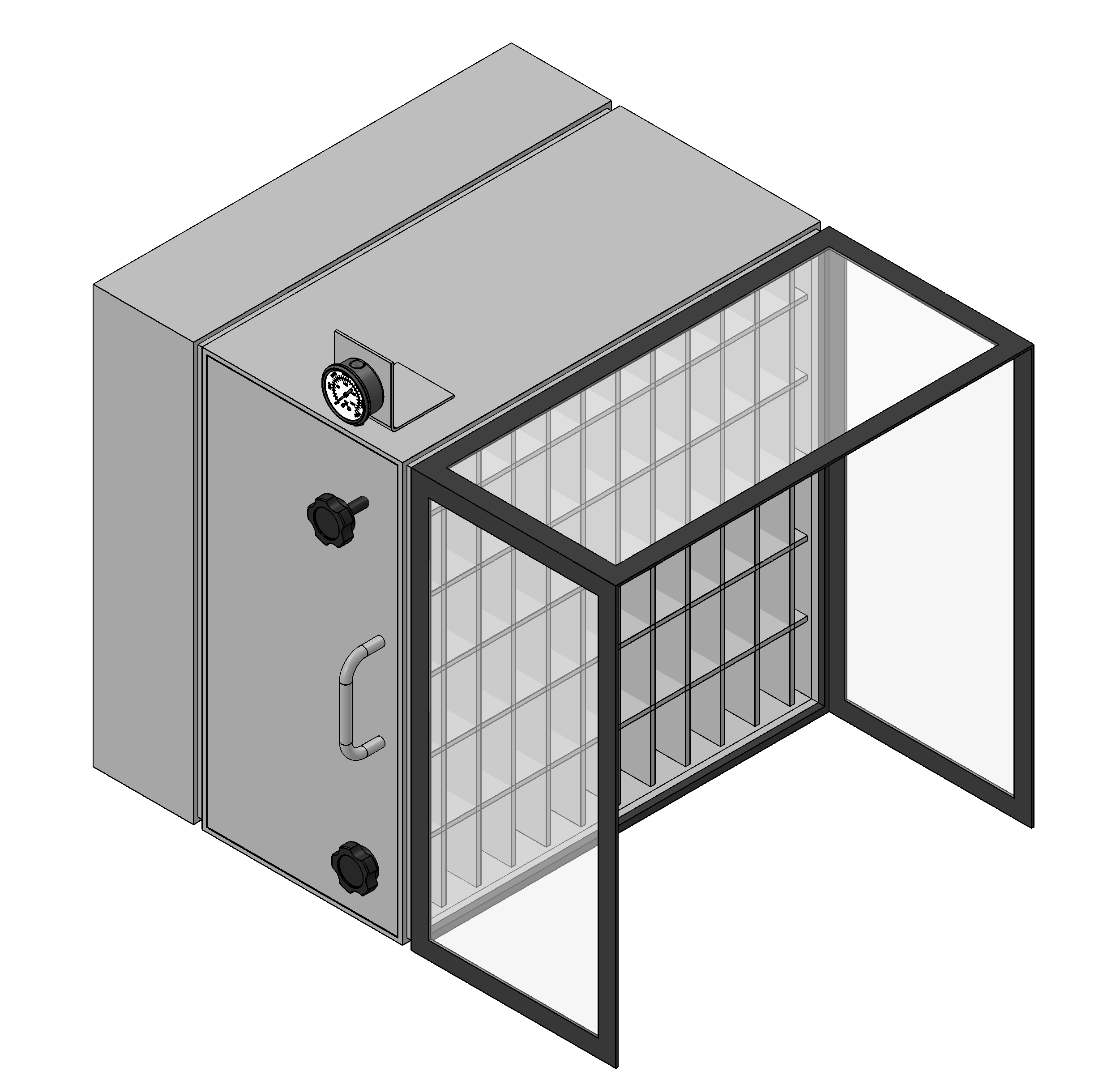
Advantages of Custom Exhaust Hoods
- Can be adjustable or stationary, requiring a minimal amount of space
- Often, they can be attached to a flexible extraction arm so they can be easily maneuvered out of the way
- Custom designed to maximize collection efficiency at a point source
- Fit to process equipment layout for dust and fume removal
- Can be added to an existing central dust or fume collection system if the exhaust fan has the performance capacity
- Isolate pollutant points throughout a plant
- Construction options of carbon steel, stainless steel, FRP, or PVC
Avoid Poor Exhaust Hood Design
- If the hood is not designed to be positioned close to the contaminant source or positioned in a correct manner it will not collect dust or fume effectively
- If the capture velocity and hood size are not correctly designed, they will not be used
- When the staff says a hood is “not working”, it will not be used
- If the hood design is “in the way” it will not be used
- Room cross drafts, caused by local cooling fans or window fans, may push air away from the hood inlet and negate the effectiveness of source capture
We are familiar with many source capture hood applications requiring atypical designs and the necessary design steps needed for the proper collection of smoke, dust, and fume. Call us and see how we can help.