Welding Exhaust Systems
Weld smoke or weld fume is a common metalworking byproduct in industrial manufacturing plants, metal fabrication shops, and technical training schools. They can be a small amount in an isolated machine shop or a major “blue haze” issue to be addressed in mass production of assembled metal fabrications. Concerns might be worker safety, equipment maintenance requirements, capital costs or simply to remove the accumulated smoke at the ceiling or roofline.
SysTech provides weld shop ventilation systems with the application of a variety of industrial ventilation equipment such as mobile or stationary dust collectors, downdraft benches, and walk-in enclosures that are designed to meet each client’s specific operational requirements.
Weld Smoke and Fume Dust Collectors
- Portable filtration units are mobile and small enough to navigate small spaces. They use either pulse clean cartridge filters or throw away panel filters, depending upon loadings and required frequency of filter change. They typically have a flexible fume extraction arm with a hood and are available in several lengths. In a small shop or if there are multiple isolated locations within a facility that need weld smoke exhaust cleaning, mobility is important, and that’s the way to go.
- A complete welding shop ventilation system with dust collector, exhaust fan, duct, hoods, and fume extractors. These are source capture exhaust systems with a cartridge dust collector and exhaust fan located remotely, ducted to slotted hoods, backdraft hoods, or fume extraction arms positioned at each weld station or point.
- Welding downdraft benches provide a work area or station to position the work assembly and can be standard construction or custom designed for heavy pieces. These benches can be structurally reinforced for heavier pieces, modified for crane access, square feet of surface work area can be increased, or have a backdraft hood built into the bench. Because of the number of atypical requests, Custom does not mean expensive or long lead time. Filtration systems located within or adjacent to the bench can be compressed air continuous “pulse cleaning” for heavy dust loadings or filter systems with throw-away filters for intermittent light-duty applications. If a bench is a perfect solution but loadings are heavy, it can be ducted to a cartridge dust collector.
- Welding walk-in enclosures are stand up or bench seating styles depending upon the piece being processed. These enclosures can be very large to accommodate large workpieces. Height and width and depth are all adjustable options.
- Custom slotted backdraft hoods designed for the products with adjusted height and width.
- Fume extractor arms provide flexibility with a workspace radius of 25 feet or more. Arms can be adapted with specialty hoods to promote maximum capture. If you’re handling large pieces, fume extraction arms fitted to a central weld exhaust system will allow access to all parts of the assembly.
Why Exhaust Systems for Welding is Important
Workers in welding operations are in continuous contact with potentially hazardous weld fumes and gases. Weld processes such as shielded metal arc welding and flux-cored arc welding produce various types of hazardous small particulate chemical compounds.
What are the hazards of welding smoke and fume?
- Weld smoke fume is made up of 30 to 80 percent submicron-sized particles. Without a reliable weld smoke collection system, these particles remain suspended in the air and are inhaled.
- Hazardous gases can be produced during welding. A weld smoke collector helps to remove toxins from the air.
- Welding stainless steel (Hexavalent Chromium) is now governed by OSHA Standard 29 CFR1910.1026 where the permissible exposure limit (PEL) for Cr (VI) is 5 µg/m³.
Plasma & Laser Cutting Table Smoke and Fume Collection
Another metalworking operation that generates smoke and fumes is the thermal cutting processes of plasma and laser cutting table operations. Remote central dust collection systems with exhaust ducts and spark arrestors are typically applied to plasma and laser cutting tables because of the quantity of micron-sized particulate. The dust collector is typically a cartridge type with nanofiber filter media with a flame-retardant treatment.
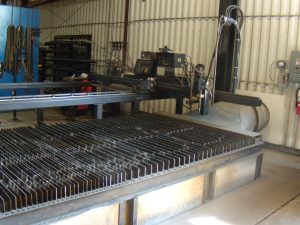
Plasma cutting table equipped with a dust collection system
What are the hazards of thermal cutting smoke and fumes?
- Plasma cutting smoke fume is made up of 10 microns or smaller particles.
- Laser cutting particulate is mostly 1 micron or less in size.
- Depending on what materials are being processed, airstream constituents may include metal vapors, metal oxides, heavy metal hazardous compounds, oxides of nitrogen, and hexavalent chromium.
- A fume collection system is mandatory in both cases, as these particles remain suspended in the air and pose a potential health hazard to workers.
We know that safety is always first and foremost, but if production is important and low maintenance a requirement, let SysTech design your next Welding Exhaust or Plasma Table System solution, and all-important criteria will be met.