“Where There’s Smoke…Expect a Fire!”
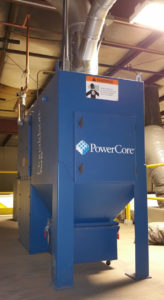
Donaldson torit PowerCore TG Series dust collector selected with flame-retardant filters for a hand grinding application.
Heavy grinding of stainless steel results in the generation of smoke, sparks and debris. A stainless steel parts fabricator in Pittsburgh had a dust collection system installed, comprised of three downdraft work stations, duct and a bag-style dust collector. The smoke and particulate was collected but the issue of spark protection and fire prevention was never addressed. The client did have operational procedures in place to prevent fires but those procedures failed to prevent two ensuing fires in their dust collector. Our challenge was to capture, convey and clean the airborne particulate, maintain cleanliness at each grinding station and provide fire protection.
The two dust collector fires the client experienced were responded to by local emergency fire services. Each event impacted production and brought negative attention to the manufacturer from local fire marshals. The client contacted SysTech to implement a solution, combining dust collection and fire protection methods to ensure no further events would occur.
Important Considerations for a Dust System with Sparks
Our design addressed multiple components of the dust collection system:
- Inspection of the work stations/capture hood for effective capture.
- Redesigned ductwork for proper conveying of the captured dust.
- Removal of sparks from the airstream via an inline mechanical device.
- Clean the dirty airstream with a continuous duty dust collector specifically designed for small micron sized smoke particles and high temperatures.
- A CO₂ fire mitigation system in case a spark bypassed the inline spark cooling device and entered the dust collector
The fabrication facility was laid out with the grinding area at ground level and the dust collector positioned on the overhead mezzanine. The collection efficiency of the down flow work stations was adequate but the duct system needed to be redesigned for the new dust collector. Multiple four (4) inch drops were placed at each work station to capture the smoke/sparks. These drops condensed into two (2) six (6) inch lines running back to the collector, merging at the unit’s inlet.
To remove sparks, four (4) Spark Coolers® by Blender Products were installed in the duct to remove potential ignition sources prior to reaching the collector. The Spark Cooler® is designed to remove sparks generated in metal and other low-load material processing applications, under non-explosive conditions. The Spark Cooler® creates turbulence in the air flow stream, disturbing the thermal bubble surrounding the spark and allowing the lower temperature in the gas stream to reduce the particle temperature.
The dust collector selected was a Donaldson Torit® PowerCore® Model TG-2 sized for 1400 CFM. The TG or “Thermally Generated” Series is specifically designed for collection of thermally generated dust. It has a footprint 65% smaller than traditional cartridge style collectors which was critical because of the mezzanine space constraints. The collector has a high efficiency fan, fire retardant Ultra-Web™ High Efficiency Power Pack filters as a standard and is packaged and assembled as a “plug-in” unit. Other features included a Zero-Turn Power Pulse Cleaning System, integrated electrical controls, quiet motor chamber with sound dampened liner, tool-less filter removal, and an all-welded design.
CO₂ Fire Extinguishing System
The final component was a fire extinguishing system that would act as a secondary line of defense in the rare case a spark would travel through the Spark Cooler and into the filter media. We selected a high-pressure CO₂ fire extinguishing system by Kidde-Fenwal to protect the collector. A Kidde-Fenwal Detect-A-Fire® sensor was utilized because of its superiority to standard rate-of-rise static detectors. The extinguishing system integrates a “rate compensation” design which senses the surrounding air temperature regardless of fire growth rate. Because ambient exhaust temperatures are higher than normal, SysTech provided a higher temperature threshold sensor to minimize false CO₂ system triggering – a costly system error.
The high-pressure CO₂ system as installed is comprised of a fire detector, control panel and an external 50 lb CO₂ tank that when discharged, floods the collector interior with CO₂, displacing oxygen required for combustion. The CO₂ system was selected over a “wet system” because in some cases water may not fully remove oxygen from the area and smoldering may continue to occur, leaving the potential for a second fire event. Additionally, wet systems result in subsequent downtime housecleaning and lost productivity.
To maximize system efficiency, we interlocked the CO₂ system controls and the dust collector fan control panel with a dynamic braking resistor. If a fire were detected, the system would automatically shut-down the fan and initiate the CO₂ release. Typical fan ‘spin-down’ time, the time that it takes for a fan to stop after power has been cut, is between 90-120 seconds. CO₂ buildup must reach a sufficient level in the collector to completely extinguish the fire. SysTech used the dynamic braking resistor to reserve direction on the motor and slow the fan faster than normal – in less than 30 seconds. This allowed the system to extinguish any fires in less than half the time it would’ve if the fan was allowed to spin-down naturally, potentially saving personnel, safety and preventing property damage.
After six months of heavy operation, running two shifts six (6) days a week, the system is performing as expected. The pressure drop across the Ultra-Web™ filter pack is less than 1.8’’ wg, capture at the work stations improved area cleanliness, and no fire issues have occurred – the CO₂ system has not initiated indicating that the Spark Cooler® units are functioning properly. This operation is no longer a concern for the customer – their plant, personnel, and reputation is protected by the new dust collection system design.
How can we help protect your facility? Call us at 800-456-9460 so you can feel confident that when you work with the professionals at SysTech, you will be in great hands.