Chemical plants, wastewater treatment plants and pharmaceutical laboratories are all picture-perfect scenarios of chemically harsh environments. The presence of compounds and gases such as hydrogen sulfide, ammonia, nitrogen oxides, hydrogen chloride and chlorine can be detrimental to your ventilation, or even worse, your employees. Within these harsh corrosive environments, metal painted industrial fans would corrode at an extremely high rate because of the corrosive nature of these fumes and vapors. A solution to the problem is Hartzell Air Movement’s FRP (Fibre-reinforced plastic or Fiberglass Reinforced Plastic) fans and blowers. These specialized fans are used in severe duty applications and chosen for their corrosive resistance as well as their durability.
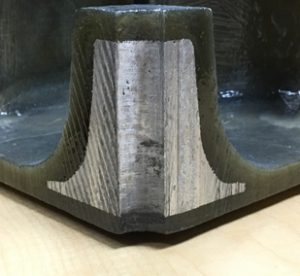
Cut section of a Hartzell FRP one-piece fan wheel
It was a new experience for me, walking through the FRP plant at Hartzell, with so many unique operations in the process. The first application to catch my eye was the large spray rooms. Within these rooms, workers fully gowned with glasses and respiratory masks, looking like there was an outbreak of some sort, were performing a process called chop spray-up. This process is used for larger FRP fan housings and is a faster method than hand laying fiberglass.
Next on my tour were the moldings. The first type of moldings I encountered were the compression moldings for smaller housings and components. Specifically, at the time I was walking through the area, they had just begun compressing components, roof curbs to be exact, for one of SysTech’s projects. The last mold process I encountered was the unique wheels in backwardly inclined and airfoil designs. Hartzell’s molded wheels differ from the competition by providing a one-piece fan wheel and thus having a stronger and more consistent product. Even the only metal piece in the wheel, the hub, was encased in the mold ensuring all pieces of the wheel exposed to the corrosive airstream were protected with resin.
Once the wheels are constructed, they are taken to be balanced. All other FRP competitors utilize drilling into the wheel and adding weights to balance the wheel, but that method adds stress and therefore weakens the wheel. Hartzell delivers a strong and precise wheel by utilizing a two-plane balance. It was interesting to observe the wheel being pushed to its specified limits and run at high speeds ensuring an effective and quality product.
A side view of a section of a Hartzell FRP one-piece fan wheel
Fans were not the only FRP ventilation equipment being constructed. I also was able to observe the assembly of fiberglass louvers and multi-blade dampers. Hartzell doesn’t stop at just centrifugal fans; they produce various types of axial exhausters as well. Important additional options they also provide are the special coatings: HartKoate, Hi-Cor and Electrical Grounded. These are designed specifically for even more difficult environments of abrasion, corrosion and static charge or explosion.
My time at the Hartzell plant was short, but very informative. The facility was well maintained, and the people were great, but most importantly, it was amazing to observe the construction of high-quality products like Hartzell’s FRP product line.
When selecting a fan that will need to withstand harsh chemicals, talk to the experts at SysTech Design. We’re available at 800-456-9460 to discuss your best options for durable, long-lasting fans.